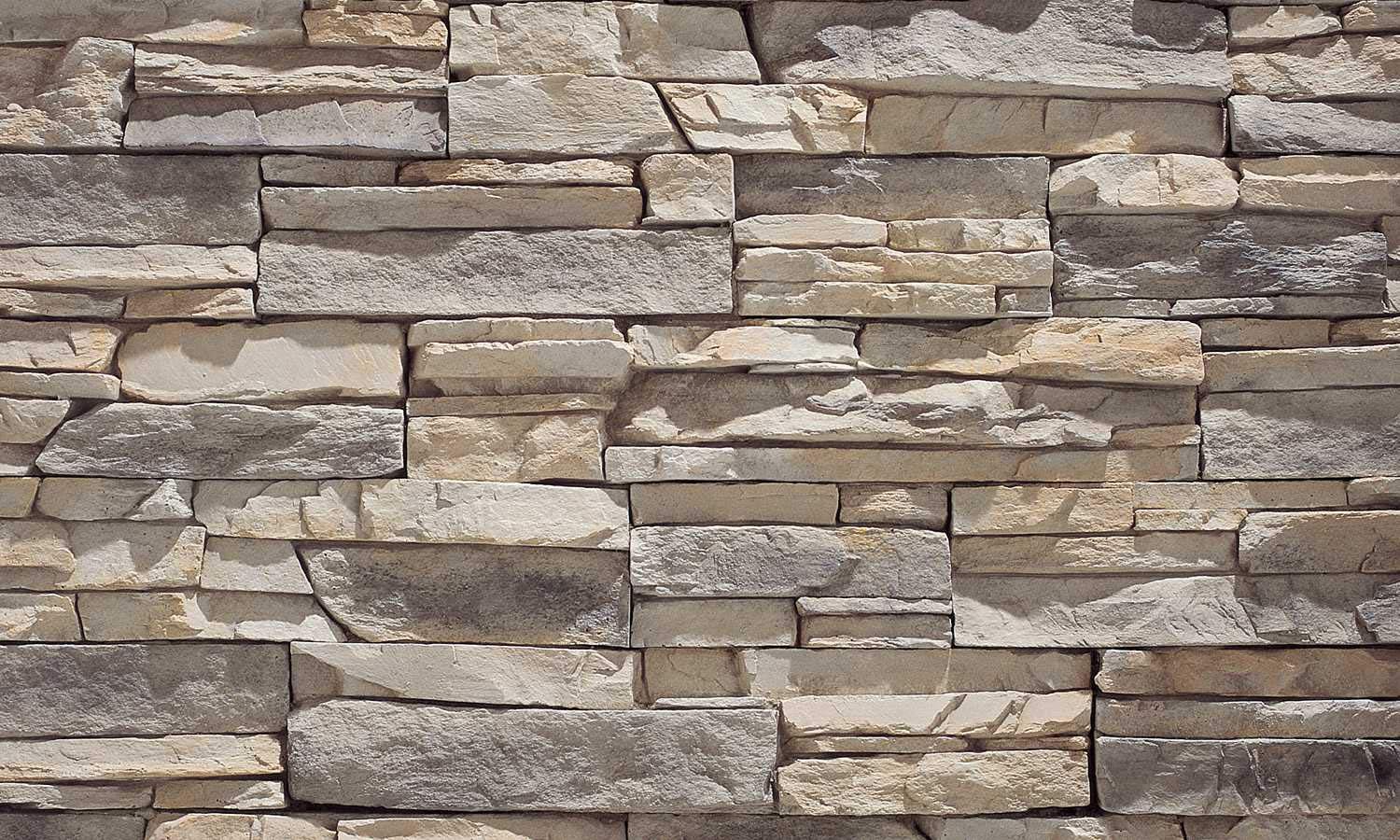
Stone
Eldorado Stone - Alderwood
Eldorado Stone - Castaway
Eldorado Stone - Dark Rundle
Eldorado Stone - Whiskey Creek
Eldorado Stone - Banff Springs
Eldorado Stone - Whitebark
Texas Stone Designs - Graphite Ledgestone
Texas Stone Designs - Alamo Limestone
Texas Stone Designs - Charcoal Luxroc
Texas Stone Designs - Mesquite Stack Stone
Texas Stone Designs - Aspen Country Ledge
Texas Stone Designs - Mountain Fieldstone
Cultured Stone - Lake Tahoe
Cultured Stone - Earth Blend
Cultured Stone - Palisades
Cultured Stone - Aspen
Cultured Stone - Gunnison
Cultured Stone - Wheaton
Cooper Stone - Alaska Flagstone (Natural)
Cooper Stone - Coffee Flagstone (Natural)
Cooper Stone - Texas Tan (Natural)
Cooper Stone - Java Ledgestone (Natural)
Coronado - Creek Rock SW Blend
Coronado - Barnwood - Old Frontier
Coronado - Texas Rubble Texas Cream
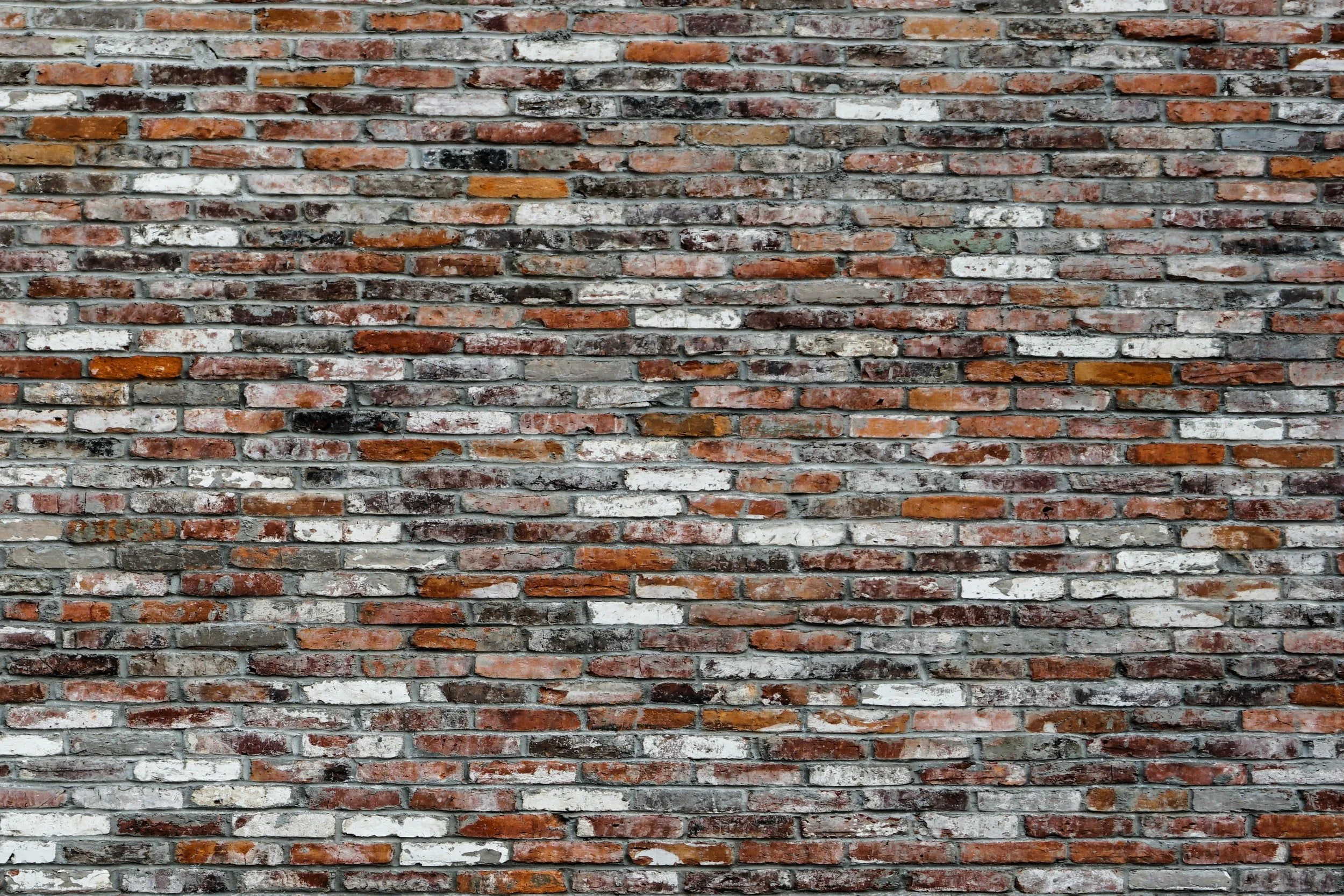
Natural & Manufactured Stone
Tascosa Brick offers a large variety of natural and manufactured stones that can be used in many different indoor and outdoor projects. Because we carry both natural and manufactured stone, there is an assortment of styles available. There are also various types of finishes offered for enhancing the look of natural stone or creating a different texture. These finishes include polished, honed, flamed, and saw cut. Be sure to estimate the amount needed for your next masonry project and view our answers to frequently asked questions about manufactured stones below.
Natural stone finishes
There are various types of finishes for natural stones including a polished finish, honed finish, flamed finish, and saw cut finish. Each type can add a special touch to your next masonry project.
A polished finish can only be done on crystallized stones and does not affect the porosity. This finish is popular because it enhances the markings and color of the natural stone material. Areas with a polished finish are reflective and very smooth. This finish is most often used in reception areas, where granite, marble and other harder limestones are placed.
A honed finish, unlike a polished finish, is not reflective. This type of finish offers a smooth surface with minimum light reflection. Often used on areas where heavy traffic would wear off a polished finished, a honed finish is also used in interior wall coverings.
Flamed finishes are a rough texture used mostly on vertical applications and floor tiles. Vein patterns and color varies from one stone to another.
Natural stone styles
Saw cut and chopped finishes owe their name to the saw cuts that are created on the surface of the stone. Once the stones are broken free of the cut layer, they are shaped to size. This finish offers a complementary accent to other types of stone work and is most often used for gate entries, walls, landscape design, and patios.
FAQ
-
Vibrated in rubber-like molds and wet cast, manufactured stones are a mixture made of lightweight sand or gravel and cement. The molds are made by being cast from real stone to reproduce the same shape and texture. Before the mixture is poured into the rubber-like mold, the mold has color treatments which are absorbed into the mixture, creating a face that looks like real stone.
-
Manufactured stones are about 8-10 pounds per square foot and one to three inches thick, depending on the style.
-
Existing applications appear to have no undesirable changes in color after years of weathering.
-
Base color is blended throughout the whole stone. However, color overtones are applied and integrated into the building material during the molding process.
-
Manufactured stones are cast from hundreds of individual molds. This method eliminates repetition.
-
Installation costs of manufactured stone can be less than the installation costs of natural stone. Manufactured types require no foundation, footings, or wall ties. Therefore, installation time is reduced considerably.
-
Occasional rinsing will remove surface dirt and dust from stones, if desired.
-
Yes, manufactured stones can be easily cut or trimmed with wide-mouth nippers, masonry saws, or a hatchet.